Navigating Import Certifications: How to Ensure Compliance for Best Food Service Equipment
In the ever-evolving landscape of the food service industry, navigating import certifications for food service equipment has become a critical concern for operators aiming to ensure compliance and maintain high standards of quality. According to a report by IBISWorld, the food service equipment manufacturing industry in the U.S. is expected to surpass $18 billion in revenue by 2024, with compliance regulations playing a significant role in market dynamics. The necessity for adherence to safety and performance standards is underscored by data from the National Sanitation Foundation (NSF), which highlights that 87% of food service businesses experienced an inspection-related issue due to non-compliant equipment. As businesses strive to thrive in a competitive market, understanding the intricacies of import certifications is essential not only for legal compliance but also for fostering trust and ensuring operational efficiency in food service equipment.

Understanding the Importance of Import Certifications for Food Service Equipment
Import certifications play a crucial role in the food service equipment industry, ensuring that products meet safety and quality standards before they reach consumers. Compliance with these certifications not only protects public health but also enhances brand integrity and consumer trust. Understanding the specific requirements for import certifications can be a complex process, but it is essential for companies aiming to succeed in the competitive food service market.
Tip 1: Research the specific import certification requirements for your target market. Each country may have different regulations, and being informed can save your business from costly delays and potential penalties.
Tip 2: Collaborate with reliable suppliers who can provide certified products. A strong partnership with manufacturers who understand the importance of compliance can streamline the import process and keep you aligned with industry standards.
Tip 3: Stay updated on changes in regulations and certification processes. Industry standards are constantly evolving, so maintaining an awareness of new developments will help you adapt and ensure ongoing compliance in your operations.
Key Compliance Requirements for Food Service Equipment Imports
When importing food service equipment, understanding and adhering to key compliance requirements is crucial to ensure smooth operations and to avoid potential legal pitfalls. First and foremost, importers must familiarize themselves with safety and health regulations established by authorities such as the FDA and USDA. These regulations often include specific standards regarding materials, safety features, and the hygienic design of the equipment. Regularly checking these guidelines can help importers stay compliant and avoid delays in the import process.
Additionally, proper labeling and documentation play a significant role in compliance for food service equipment imports. Importers should ensure that all incoming products are accurately labeled with the necessary certifications, such as NSF and UL marks, which indicate that the equipment meets safety and performance standards. Furthermore, maintaining comprehensive records of all import transactions and compliance checks can serve as a safeguard, protecting businesses against fines and ensuring a seamless import experience. By prioritizing these compliance requirements, importers can navigate the complexities of the food service equipment market with greater confidence.
Step-by-Step Guide to Obtaining Import Certifications
When it comes to importing food service equipment, ensuring compliance with import certifications is crucial for businesses aiming to succeed in the competitive food industry. The process may seem daunting, but breaking it down into clear steps can significantly streamline your efforts. Start by identifying the specific certifications required for your products, which can vary by country and equipment type. Research the regulatory guidelines provided by local authorities and relevant international organizations to ensure you have a comprehensive understanding of the standards your equipment must meet.
After establishing which certifications are necessary, the next step is to gather the required documentation. This often includes product specifications, safety certifications, and proof of compliance with health and safety regulations. It’s essential to collaborate with suppliers who can provide the necessary documentation as you prepare your import application. Once your application is complete, submit it to the appropriate regulatory agencies and be ready for inspections or additional requests for information. By following these steps meticulously, you can facilitate a smoother import process and position your business to thrive in the food service equipment market.
Common Pitfalls to Avoid When Navigating Import Compliance
Navigating import certifications can be a minefield for businesses importing food service equipment, especially when it comes to compliance. One common pitfall is misunderstanding Incoterms, which are critical in defining responsibilities and liabilities in international trade. According to industry reports, more than 30% of importers incorrectly apply Incoterms, leading to costly delays and compliance issues. For instance, the use of EXW (Ex Works) can place undue risk on buyers who may not be fully aware of local regulations and certification requirements.
Another frequent mistake involves failing to properly document compliance throughout the import process. A recent study indicated that 40% of import-related audits reveal gaps in documentation, primarily due to inadequate understanding of local certification standards. Compliance with certifications not only prevents legal penalties but also enhances product credibility in the market. Ensuring that all documentation is accurate and comprehensive can significantly mitigate the risks associated with non-compliance and build trust with consumers. Prioritizing these areas is crucial for businesses aiming to thrive in the competitive landscape of food service equipment.
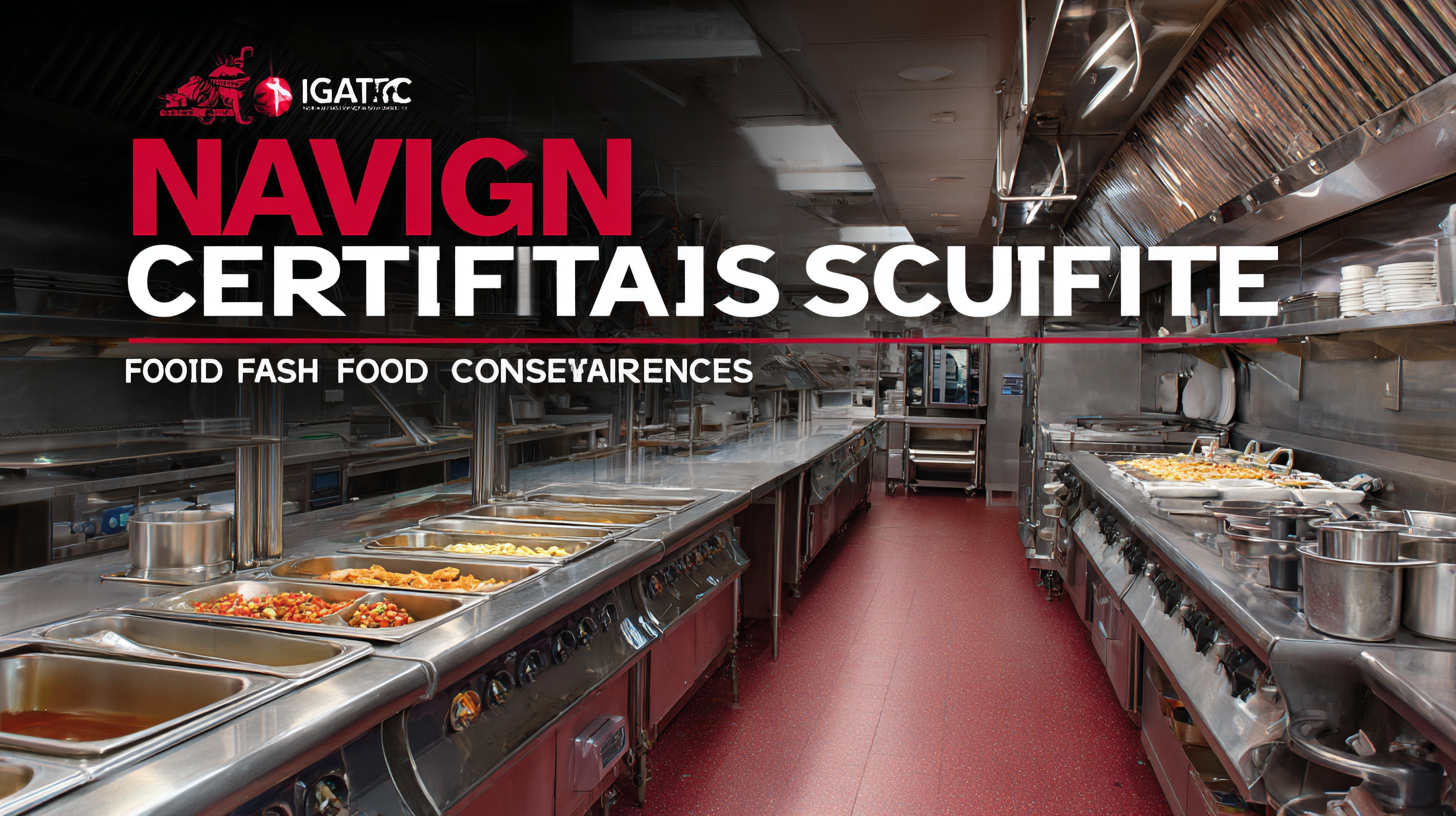
Best Practices for Maintaining Ongoing Compliance in the Food Service Industry
In the competitive landscape of the food service industry, maintaining compliance with
import certifications is crucial for businesses looking to thrive.
According to a report by the Global Food Safety Initiative (GFSI), approximately
70% of food service operators reported challenges in adhering
to international food safety standards. This underscores the importance of establishing a robust compliance framework
to avoid costly penalties and operational disruptions.
To ensure ongoing compliance, businesses should implement a systematic approach.
Tip: Conduct regular audits to assess adherence to import certifications and safety regulations.
The U.S. Food and Drug Administration (FDA) recommends that food service operators familiarize themselves with the
Hazard Analysis and Critical Control Points (HACCP) system, which
can significantly enhance food safety management.
Additionally, training staff on compliance protocols is vital.
Tip: Organize workshops that focus on the latest regulations and best practices in food safety.
The National Restaurant Association highlights that well-trained employees are
60% more likely to adhere to compliance standards, thereby
reducing the risk of violations and improving overall operational efficiency. By fostering a culture of compliance,
food service businesses can not only navigate regulations effectively but also enhance their
reputation in the marketplace.
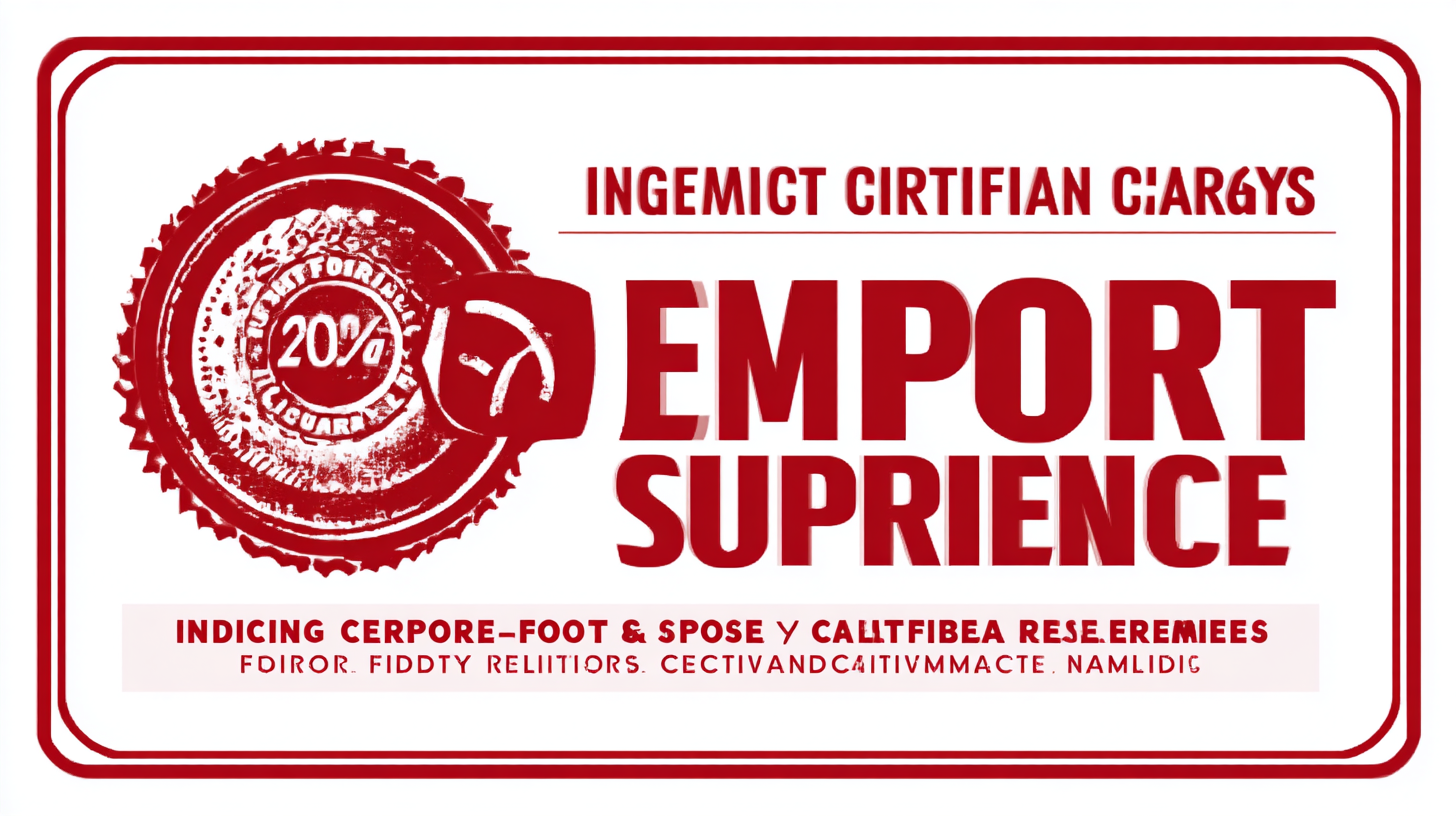